We’ve had an ongoing discussion on our internal message board SARC-all about nixie tubes, vacuum fluorescent displays and designing circuits to drive them. One of our members, Mike AC9CG, has a long history working for a VFD manufacturer and compiled a very nice history and technical overview of the devices. His notes follow. –Ed.
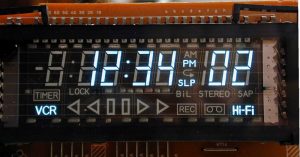
VFD Sales in USA
- From around 1970 to 1997, there were 3 Vacuum Fluorescent Display (VFD) manufacturers, and they were all Japanese: NEC Electronics, Futaba Corp and Noritake Corp.
- The 2 top VFD manufacturers were NEC and Futaba Corp, who produced VFD (displays) for appliance, automotive, Consumer electronics (VCR and AV equipment) and point-of-sale terminal applications, and the much smaller Noritake Corp, who produced mostly just point-of-sale terminal displays (for gas pumps, cash registers, etc.). NEC Electronics also had a full line of semiconductors, including 4bit microcomputers that could directly drive 40Volt VFDs and high voltage driver ICs capable up to 120VDC VF drive.
- Since most of the VFD customers for USA were in Chicago area, all 3 Japanese VFD companies had/have main sales offices and VFD technical support in Chicago’s northwest suburbs:
- NEC Electronics at 7200 W. Higgins, Hoffman Estates, IL. Note that NEC’s trade name for VFD panels was FIP (Fluorescent Indicator Panels) but they were exactly same technology as VFDs
- Futaba Corp at 711 E State Parkway, Schaumburg, IL
- Noritake Co. located at 2635 S Clearbrook Dr., Arlington Heights, IL
- From 1985 to 1997 I was NEC Electronics Field Applications Engineer in Chicago area supporting technical aspects for ICs and VFD panels at major VFD customers ACT (Appliance Control Technology), DAC (Digital Appliance Control), Eaton Corp (appliance controls), Spitfire (appliance controls), Motorola Automotive in Northbrook and other smaller VFD customers. These appliance control sub-contractors designed, wrote MCU software and manufactured just the electronic control keypad/panel/display modules for big appliance companies: Whirlpool, Maytag, Amana, Electrolux, GE Appliance, Bosch-Siemens, etc., in the USA.
- At Motorola Automotive in Northbrook, Ted (AB9SZ, long-time SARC member) was a staff scientist and key advisor to the Motorola design engineers we were working with for Chrysler Car dashboard using VFD displays.
- In 1997, NEC stopped manufacturing VFD (FIP) panels, since we were losing money making them (described as negative profit situation by the Japanese!). We sold our whole VFD production line equipment and portfolio to Samsung in Korea. However Futaba and Noritake still produce VFD panels to this present day.
- Starting in 1998, NEC ended up selling 3 high voltage driver ICs per display board to Futaba Schaumburg for a VFD 80×16 dot matrix module used for a Trip computer in Jeep Grand Cherokee models. That design netted NEC about 250K-300K driver sets (3 ICs each) per year times $5.00 per display module (about $1.25Million-$1.5Million per year sales for NEC) and that ran for about 10 years. I was involved heavily in the technical support for these NEC high voltage driver IC product at Futaba Schaumburg.
VFD technical details
- VFD display has similar technology to Audio/RF signal Vacuum tubes, except a VFD panel only has filaments, multiple grids and multiple anodes. VFDs have NO cathode whereas most audio/RF signal, receive and transmission Vacuum tubes do have a cathode.
- Instead, a VFD panel emits electrons that travel directly from the filament to the selected Anodes, gated by one digit grid gating control at a time, with some anodes ON and some anodes OFF during each grid enabling time (one grid per digit)
- Most VFD panels are multiplexed, meaning that usually a multiple digit display only has one digit enabled at a time, using one grid line per digit, and all the corresponding common anodes are wired in parallel. For example a simple appliance type VFD might have 5 total digits and 12 segments per digit. Without multiplexing, a 5 digit, 12 anode VFD panel package might need over 64 pins (5×12=60 anode pins, 1 grid pin, and 4 filament pins) and require a high voltage driver IC with over 64 pins, quite expensive. Multiplexing reduces that pin count in my example to about 21-22 pins (5 grid lines, 12 anode lines, 4 filament lines) and the high voltage driver IC can probably be less than 24 pins. (17 high voltage lines, multiple power supply and ground lines)
- There is a very simple version of VFD panel using a static drive, without multiplexing, but usually this VFD display type might only have 2 digits of 7segments each, with very limited functionality!
- One downside of the multiplexed VFD panel is that the anode segments get visibly dimmer as the multiplex level increases, so the grid and anode drive voltages need to be increased to maintain a certain brightness level. For example, in the 5 digit display each digit is only energized for 1/5 (or possibly 1/6) of the total display refresh time. However, for a 20 digit display, each digit is only energized 1/20 (or 1/21) of display refresh time. Consequently, a 20 digit display might need a 50V-60V voltage drive level, versus a 5 digit display might be driven at 25V-30V drive level.
- The typical VFD display filament consists of 3 or more parallel filament wires running in the longest dimension of the VFD panel, typically horizontally. You can usually spot them in front of the digit segments with display un-powered. However their glow is very faint and hard to see unless you view the powered VFD panel in a totally darkened room. By contrast an audio/RF Vacuum tube has a very bright filament you can see in daylight when tube is powered on.
- All audio/RF/CRT vacuum tubes and VFD (a.k.a. FIP for NEC) panels all use a “Getter” to help eliminate bad effects of residual gases and water vapor, mainly the H2O vapor. Even the best vacuum pumps probably only achieve one-one thousandth of an atmosphere reduction in gas/water vapor remaining in the “vacuum”. The getter is a chemical introduced into the Vacuum tube or VFD panel after air evacuation, but before the hot, molten tube glass nipple is sealed closed. Later an inductive RF probe is placed near the Getter spot, elevating the getter chemical temperature to several hundred degrees. This causes a majority (but not all) of the residual gases and water vapor to be combined with the getter chemical.
- For NEC Electronics, we manufactured VFD/FIPs at Izumi City, Kyushu, Japan which is in a tropical area having a latitude similar to Tampa or Miami, Florida, with high temps and high humidity in summer months. Therefore we had to take great care in eliminating Water vapor contamination effects especially during the summer months, as it was too expensive to Air condition factory buildings where there were many open flames to melt display glass to a pliable or liquid state.
- For a Vacuum tube or VFD tubes with good vacuum seal, the Getter can be seen as a small dark or silverish spot inside the glass envelope, with a spot size something between pea-sized and dime-sized. If the vacuum is lost, or seal of evacuation nipple is broken, the getter spot will turn totally white. If the getter spot is whitish, the VFD or Vacuum tube is damaged, and is totally inoperable. This condition is equivalent to “letting the smoke out” of a transistor. If you let the transistor smoke out, it’s permanently ruined, unfixable.
- Normally, VFD display panels are operated with Anodes and Grid control lines turned either totally ON, or totally OFF. I’ve never seen them used in a analog manner (like a signal amplifier) but it might be interesting to try it.
From 1985 to 2019, Mike worked in various sales, marketing and application engineering support roles for all NEC Electronics discrete electronic components (including VFD panels) and Integrated Circuit products, especially Microcomputers. In April 2011, NEC Electronics merged with Renesas Technology (previous 2003 merger of Hitachi and Mitsubishi semiconductors) and was renamed Renesas Electronics, becoming the largest Japanese semiconductor manufacturer. Mike retired from Renesas Electronics in August 2019 after 34+ years at the combined NEC/Renesas company
-Mike AC9CG
Photos
The photos have been provided for a visual reference. They are not necessarily the products described above.